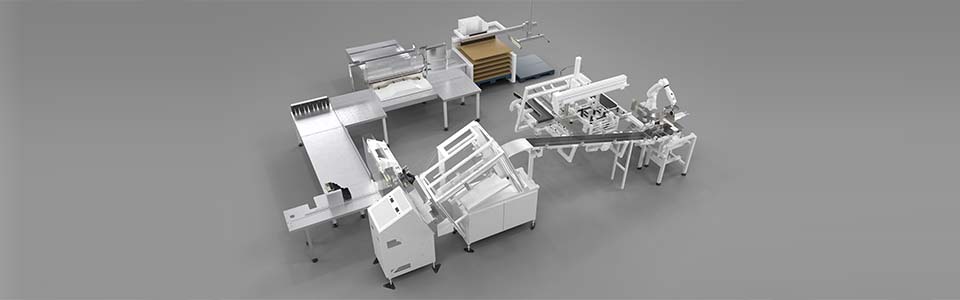
POLAR LabelSystem DC-12 RAPID
Fully autonomous system for label production: from the cutting layer to the ready-to-ship tray
POLAR LabelSystem DC-12 RAPID is the most productive die-cutting system from POLAR for highly automated, operator-free inline production of bundled die-cut and cut labels. The individual production steps, including the final packaging, are carried out without an operator.
With synergies in the development between POLAR and the packaging specialist DIENST, a fully automatic, operator-free process was developed – from the sheet to the tray. RAPID stands for Robotics for Autonomous Processing of Industrial Die-Cut Labels.
Most efficient system on the market
The highly efficient POLAR LabelSystem DC-12 PLUS, which at 1440 bundles per hour is the fastest system on the market, was the basis for the new development. Further, sophisticated automation components help the proven system for processing die-cut labels to new top performances. These components consist of a system for automatic loading of cutting layers, an automatic cutter for fully automatic cutting of strips and, at the end of the workflow, a sorting and packing station that picks up individual bundles by robot, turns them and places them sorted in the tray.
In the LabelSystem DC-12 RAPID, the robot takes over what is usually a manual process of packing 24 label bundles per minute.
High ergonomics
In addition to the efficiency aspect, this also eliminates the physical strain of manual packaging. In general, the high degree of automation of the system promises the best possible ergonomics, as manual interventions during production are eliminated.
Job change at the push of a button
New components are operated via an HMI that meets the latest industry standards. Inputs and format settings are intuitive and easy to handle.
Setup times are minimized. Job management is available for repeated jobs. A format change takes only 15 minutes thanks to the menu-guided job change, the format memory and POLAR OptiChange - the patented change frame system. OptiChange reduces make-ready times by allowing large parts of the job change to be prepared outside the machine.
Future-proof technology
The future-proof new industrial control system enables remote service (remote diagnosis and maintenance) for further improved machine availability and integration into the digital workflow. Interfaces for the acquisition of data such as downtimes, die-cutting strokes, etc. are provided.
Workflow:
- The counted and pre-jogged layers are being taken from an automatic Air-Board Lift onto the rear table of Automatic Cutter POLAR 137 Autotrim-M that cuts them into strips
- Strips are conveyed to the loading table of the AC Autocut 25 PLUS (part of the POLAR DC-12 PLUS), where they are being cut according to label size, either single strips or two strips at once into label stacks
- The punching stamp pushes the stack through the System Die-Cutter DC (puncture principle) where the stack is given its intended shape
- After die-cutting the label stacks are automatically pushed to the Single-Station Bander BD where they are banded
- The banded labels are packed by a robot in cartons or trays, ready for dispatch
Single strip | Double strip | |
Label size, min. | 20 x 40 mm | 20 x 40 mm |
Label size, max. | 170 x 210 mm | 120 x 120 mm |
Die-cut format, min. | 16 x 36 mm | 16 x 36 mm |
Die-cut format, max. | 166 x 206 mm | 116 x 116 mm |
Clamp opening, min.-max. | 35 - 120 mm | 35 - 120 mm |
Height of cutting-die, min-max. | 50 - 100 mm | 50 - 100 mm |
Max. performance per minute | 18 cycles | 12 cycles |